Hello Mr. Thanh! Can you please share your career path?
I graduated with the Paper Manufacturing Technology major, Forestry Faculty, Nong Lam University in Ho Chi Minh City in 2009. Then, I worked for an office paper mill in Binh Dương Province for a month before joining Saigon Paper in September, 2009.
At first, I worked as a shift worker of the wastewater treatment operation team of My Xuan Factory 1. Then I was transferred to the wastewater treatment operation team of My Xuan Factory 2.
In 2011, I was moved to a project team in which my role was supervising the installation of Tissue Machine 6 (TM6). After the installation was complete, in March 2012, I joined operating this machine with the consultancy of foreign professionals and senior colleagues.
In June 2012, I became technical staff of the Technical Service Section.
In March, 2014, as senior staff of TM6 left the job, I was assigned to take this role. Four months later, I was promoted to Line Technician at TM6.
In late 2016, I was promoted to TM6 Machine Leader.
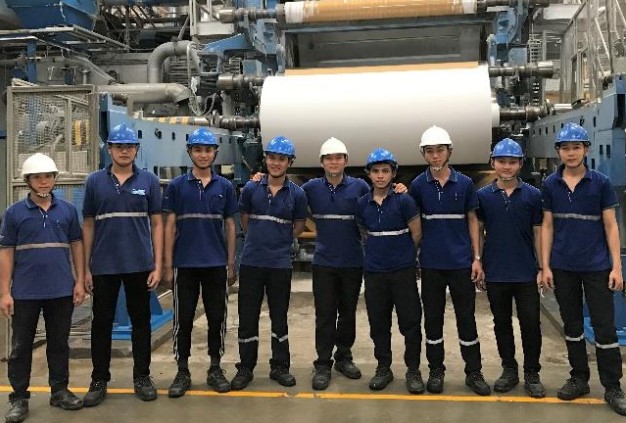 Mr. Thanh (middle) and his team members posed for a photo in front of TM6
How many employees you are managing?
What is your typical working day like?
Currently, I manage 28 people.
I begin a working day by checking the schedule of meetings and setting targets to complete within the day.
Then, I’ll read report emails from the shift leaders. If there is any production issue that is relevant to other teams like maintenance or planning, I’ll contact them immediately to tackle that issue.
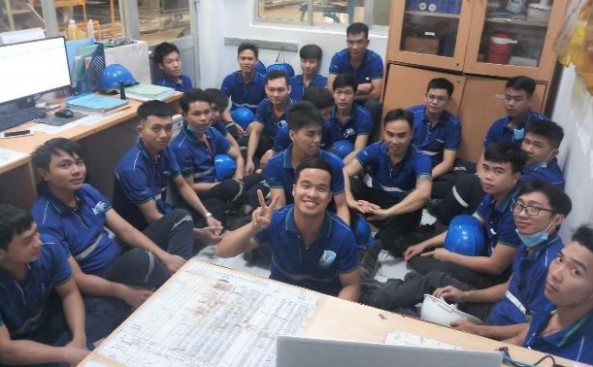 Mr Thanh (not pictured) took a photo of his team before a training session in late October, 2020
|
Next, I’ll compare yesterday’s production output with the plan. If they are same, that’s fine. But if the output falls, I’ll study the cause of the problem.
For example, I discover the decrease in output originates from the fact that paper is cut during the production process and the root cause is that the frequency of cleaning the chemical filtration equipment has not been specified. As a result, sometimes the filter is blocked, making the chemical not be pumped into the paper-making process. To fix this problem, I regulate the frequency of cleaning the filter and put it into the check list. I also follow and remind our team members.
Next, I’ll read statistical reports on the consumption of electricity, steam, chemicals, etc. during the production process. If there is any actual index different from the norm, I’ll look into the cause to solve the problem and report to my line manager.
Next, I’ll look at tomorrow’s production plan, specifically checking the type of paper, whether standard specifications for producing that paper type, and important points to remind staff.
Besides, I often observe the shift leaders, senior staff and workers so that I can timely guide them how to work more efficiently and remind them to comply with the check list and procedure. Finally, I’ll make a report and send it to my manager.
Can you talk a little bit about your hobbies?
I often play football to improve health. Previously, I joined a football team that consisted of many people from other companies in My Xuan A Industrial Park. Since a month ago, I’ve called TM6 team members to play football together every week to enhance our relationship.
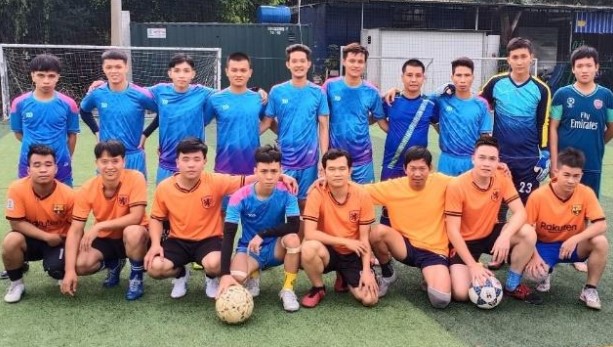 Mr. Thanh (sitting, 4th from right), his colleagues and other people working in the industrial park before a match in early November, 2020
Have you ever met a big challenge during working at Saigon Paper?
Early this year, after Tet, half of my team members, mostly workers, quit their jobs. The shift leaders were worried that new workers, who had not been familiar with the job yet, might fail to meet the output. I myself thought a lot. I tried my best to list all my knowledge into the books, procedure, regulations so that new members can look at them to work on the machines accordingly. They lack paper crane and operation skills, but these things can be trained in the short time. So far, I feel happy as I have overcome the difficulties. In fact, everything has become better (smiles). |